Data strategy and 4.0 roadmap: Interview with Eva ROTHER, Managing Director of FPT Industrial France
13 October 2022How can you turn your data into a performance and efficiency lever? How can you transform it into a decision-making tool, gain flexibility and add value to your business? How to develop your data strategy to move into the 4.0 era and optimise your ROI?
Meeting with Eva Rother, Managing Director of FPT Industrial France and the Bourbon-Lancy site who testifies on the development of the group's 4.0 roadmap. Eva Rother, who has a PhD in Management 4.0, explains the group's strategy towards Industry 4.0.
Why did you set up a data strategy?
Eva Rother – Our data strategy is based on a necessary change. The time is ripe for reducing product launch times, developing process flexibility and agility, and the need for efficiency. These are all reasons for developing our business through the development of a 4.0 strategy at the Bourbon-Lancy site, in which data plays an important role.
How does it relate to an overall strategy towards Industry 4.0?
E. R. – A 4.0 roadmap has been developed since 2015 on the Bourbon-Lancy site, supported by various theses and in conjunction with the LIRIS Laboratory in Lyon. We worked for 3 to 4 years on the technological, methodological and management dimensions of 4.0. In 2019, when we tackled the maintenance part, we realised that without visualisation of our data, we would be working on projects in parallel without any real convergence. We then tried to understand the benefits they could generate along two axes, the use of the data we could have and its added value for the business, and with three levels: visualisation, analysis and decision support.
How to adapt it to your context?
E. R. – Our factory dates back to 1874 with machines that have an average age of twenty years, sometimes 40 years. We therefore had to take into account the technical heritage of our machines to see how to access the data of our production processes. We have thus carried out a mapping of the factory's priorities in terms of production, maintenance, environment, energy and logistics. With data that is either already available or to be created and those that are still difficult to obtain. It was important for us to explain the issues related to the use of data and its contribution to decision-making, because that's what we really expect today.
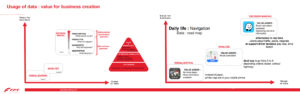
How can it be implemented, especially with regard to data collection?
E. R. – For two years, we have been working in parallel on data sourcing and thinking about their use. On the first point, rather than adding sensors, which can be costly on machining centres such as ours (it requires downtime and increases the risk of breakdowns), we sourced the existing data from the numerical control or the PLC. The objective was to find technical solutions that could be applied to a machine pool as heterogeneous and old as ours. In parallel with the collection of data, a reflection was carried out on their use: which business needs and which artificial intelligence algorithms in order to prioritise our data-centred investments.
Why did you choose data analysis and AI tools like DiagRAMS?
E. R. – It was our partner Siemens who put us in touch with DiagRAMS during the DIA (Digital Industry & Infrastructure Awards) competition organised with Atos. It was a great opportunity for FPT to present our industrial use cases to data analysis experts and to better understand how to leverage our data (see diagram). This is how our collaboration for predictive maintenance on our machining centre started.
The DiagRAMS solution allows us to analyse the precise parameters on the machine and to detect drifts in the axes and compressed air leaks. We now have a good view of the state of health of the equipment and of future breakdowns. In the long term, the aim is to extend the analyses to include product quality prediction.
Where do you stand today and what are the next steps?
E. R. – New lines with new machining centres are coming to the site for the development of a new product launched in 2023-2024. It will therefore be an opportunity to capitalise on what we have learnt with our older machines to recover data, including data concerning the product, in order to push all these algorithms and predictive analyses further on our machining centres. On the assembly part, we are working on the process of the product part. As far as cyber security is concerned, we have strictly applied the Group's protocols, even if it was not easy at the beginning because it took 18 months for the first machine, but today it only takes a few hours. In any case, it allowed the protocols to evolve by taking these new issues into account.
In addition to production, have you identified other impacts on management and the environment?
E. R. – There is a real issue around the environment and energy in a broad sense, where data is controlled manually. In the future, it is realistic to imagine monitoring the site's environmental impact in real time and to have real-time visibility on the consumption of our production lines in order to ration them. The idea is to have the panel of our process, product and possibly personal or environmental information to make the best decision, or, in any case, to have scenarios of possibilities to make it.
How to calculate the ROI on a data strategy?
E. R. – ROI is very difficult to calculate on these projects, so we have chosen to develop a roadmap based on opportunity and to work systematically to demonstrate by example the benefits of connecting our equipment. Each time, we opted for solutions where we were autonomous in our ability to connect, program, store our data, etc. To make progress on the analysis part, we have established collaborations with startups such as DiagRAMS and universities thanks to several theses that allow us to challenge ourselves on the use of data.
Is this strategy part of a general orientation at the level of your Group?
E. R. – No, it was first and foremost a desire of the site, even if it is being developed at other Group plants. All the more so as we have obtained an Agamus award on the digitalization part and have been labelled as a showcase of the future in 2018. Our experience shows that this is possible, without a big budget or changing all the processes and machines. It is above all a question of opportunity and common sense, especially when you know your processes.
How do you get the teams on board with this subject of data, which can arouse fears?
E. R. – The first step is demystification: Industry 4.0 is not going to replace humans, unlike 3.0 which led to automation. We have therefore communicated transparently to the teams on this subject. No, tomorrow's data will not replace the manager, on the contrary, our vision is that it will help free up time for his or her primary mission: people. In our company, less than 8% of a manager's time is actually spent on human-centred activities. It is therefore a question of automating tasks such as reporting and facilitating the part that concerns 20 to 30% of his workload: decision making.
What advice would you give to a company that wants to implement a data strategy?
E. R. – It is really important to understand that, contrary to popular belief, it is far from being unattainable. We need to demystify data, which is not only reserved for large groups. An SME/SMI can do this without a major investment but with common sense and small steps. This makes it possible to grow along with the technology, to appropriate it and to integrate it much more easily into the change. It is also important to bear in mind that it is not the IT specialists who own the data, but the employees in the field who master their processes. It is essential to get the teams involved in these projects so that the data serves the business and not the other way round.
About FPT Industrial
FPT Industrial France designs and produces industrial engines for trucks, buses, boats, agricultural equipment, etc. For this motorisation giant, the transition to Industry 4.0 is not a revolution but an evolution: a simple step-by-step process implemented with all employees.