L’intelligence artificielle dans l’industrie : science ou science-fiction ?
Le 24 mars 2021L’Intelligence Artificielle (IA) fait le buzz ! Qualifiée de révolution technologique du XXIème siècle, l’IA est mise à toutes les sauces dans les médias et est devenue un argument marketing de référence avec, à la clé, des promesses alléchantes en terme de gain, d’efficacité, de flexibilité…
Entre fantasme et réalité : qu’en est-il vraiment dans le secteur industriel ? Et surtout quelles sont les attentes ?
Loin de l’explosion dépeinte dans l’imaginaire collectif, l’IA arrive progressivement dans les usines. Pourquoi cette entrée en douceur ? Ce que cherchent les industriels, ce n’est pas une technologie coûte que coûte (en tant que telle), mais une réponse concrète à un problème concret.
Dans un environnement de plus en plus complexe et contraint, le besoin est de pouvoir optimiser les process, anticiper pour mieux piloter et adapter sa stratégie. Cela se traduit par la mise en place de projets au périmètre bien défini et pour lesquels l’Intelligence Artificielle doit s’inscrire dans la continuité des méthodes industrielles. En effet, l’IA apprend des données industrielles, de l’existant, et s’appuie sur l’expertise des équipes du terrain. Cette continuité et l’implication des différents acteurs sont donc essentielles.
Il n’est pas aisé de faire mieux que les experts : qu’est-ce que l’IA doit apporter en plus ?
Le vrai challenge de l’Intelligence Artificielle dans l’industrie : permettre aux équipes du terrain d’augmenter leur connaissance. Trop souvent, les solutions d’IA fournissent des informations que les équipes avaient déjà par d’autres biais, ou permettent de trouver automatiquement ce que les experts connaissaient déjà !
Dans la maintenance, la vraie avancée consiste à découvrir l’état de santé réel des équipements et à pouvoir suivre leur évolution dans le temps (suivi de tendance et de dérive). Aujourd’hui, beaucoup de solutions permettent uniquement de détecter le franchissement d’un seuil d’alerte simple. Mais recevoir une alerte pour un dépassement de seuil ne permet pas d’anticiper et de mieux comprendre l’état de santé et le rythme de dégradation des équipements. En effet, la définition d’un seuil d’alerte ne permet pas de suivre la dérive de fonctionnement dans le temps.
Par ailleurs, souvent limitées à la surveillance d’un capteur à la fois, ces solutions de suivi de dysfonctionnement ne sont pas suffisantes car elles ne prennent pas en compte les modes de fonctionnements variés de machines.
La variabilité dans le process
Pour être pertinente, une solution d’IA doit prendre en compte la forte variabilité inhérente aux process de production. Que ce soit au niveau du process global (variation des matériaux, des ordres de fabrication, des conditions extérieures…) ou au niveau d’un même cycle de production. Cette variabilité génère des variations dans le temps des conditions d’utilisation des équipements industriels. Sur une même machine, on observe des régimes de fonctionnement diffèrent en fonction du produit réalisé/traité ou de la période. Les signaux des capteurs présentent des régimes variés au niveau de leur valeur moyenne, de leur variance et cela sur tout ou partie des signaux. (schéma 1). A l’échelle d’un même cycle, on constate également des variations importantes correspondant à des régimes de fonctionnement différents (cf. schéma 2).
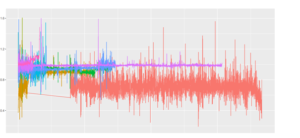
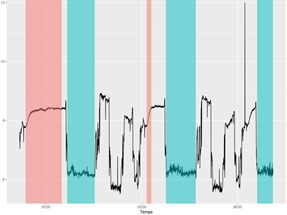
Dans ce contexte de forte variabilité de la production, la détection d’anomalies est complexe. Les fluctuations dans les signaux rendent difficile la définition de seuils d’alerte. Ils doivent être suffisamment tolérants pour accepter cette variabilité mais pas trop, au risque de manquer des alertes. L’objectif est de limiter le nombre de fausses alertes (faux positifs), d’avoir un système auto-apprenant permettant de découvrir dans le temps les seuils optimums. La plus-value de l’IA est de permettre la détection des variations et des anomalies en se basant sur la connaissance du modèle de fonctionnement pour chaque produit et chaque phase du cycle d’une machine.
IA de DiagRAMS : technologie puissante et accessible
L’intérêt de solutions comme celle de DiagRAMS, c’est justement de réaliser l’analyse multivariée de données industrielles brutes. Différents signaux (température, pression, consommation électrique, vibration…), de sources différentes (données des équipements, données de maintenance, données de qualité et données des systèmes de supervision) sont conjointement pris en compte pour obtenir des informations sur les contextes d’utilisation.
L’Intelligence Artificielle permet alors un apprentissage automatique des seuils optimums dans la durée d’alerte pour chaque mode de fonctionnement des machines, mais aussi celui des éléments caractéristiques de dysfonctionnements dans les signaux. De plus, elle permet le suivi des dérives (comment ces modes évoluent dans le temps en plus du non-dépassement de seuils).
DiagRAMS Technologies est issue de plusieurs années de R&D chez Inria, le centre national de recherche dédié aux sciences du numérique. Sa solution de détection d’anomalies en mode non supervisé prend en compte la variabilité des process et les différentes sollicitations des machines afin d’offrir d’excellentes performances. En effet, la connaissance du contexte d’utilisation est essentielle pour détecter les incidents sortant du bon fonctionnement des équipements. Cela permet de pouvoir débuter un projet sans avoir nécessairement besoin d’historique de pannes pour apprendre à reconnaître les patterns caractéristiques de dysfonctionnements. L’IA se focalise sur l’apprentissage et la découverte des bons fonctionnements, et ce, dans toutes leurs variétés.
Toute la pertinence d’une solution d’IA, comme celle de DiagRAMS, est de se positionner comme un outil d’aide à la décision, un soutien aux équipes sur le terrain qui ont le choix de mettre en œuvre les recommandations de l’IA ou pas !
Pour cela, il est important de présenter des informations remises précisément dans le contexte particulier des sites industriels. Cela permet de démontrer que le système d’IA comprend le process industriel dans lequel il opère, et contribue à créer de la confiance dans les résultats qu’il présente.
Grâce à cette approche contextuelle basée sur l’analyse croisée multi-capteurs, les utilisateurs disposent d’alertes plus spécifiques et plus riches car les dépassements de seuil ou les dérives sont caractérisés dans leur contexte d’utilisation. Si les technologies d’IA sont puissantes, c’est l’adhésion des opérateurs sur le terrain et leur appropriation des solutions avec une réelle plus-value qui permettront véritablement de faire entrer durablement l’intelligence artificielle dans les usines.
Jean-François Bouin et Margot Correard